Warehouse Optimization: How Barcodes Improve Your Inventory Management
By Rackbeat February 21, 2025
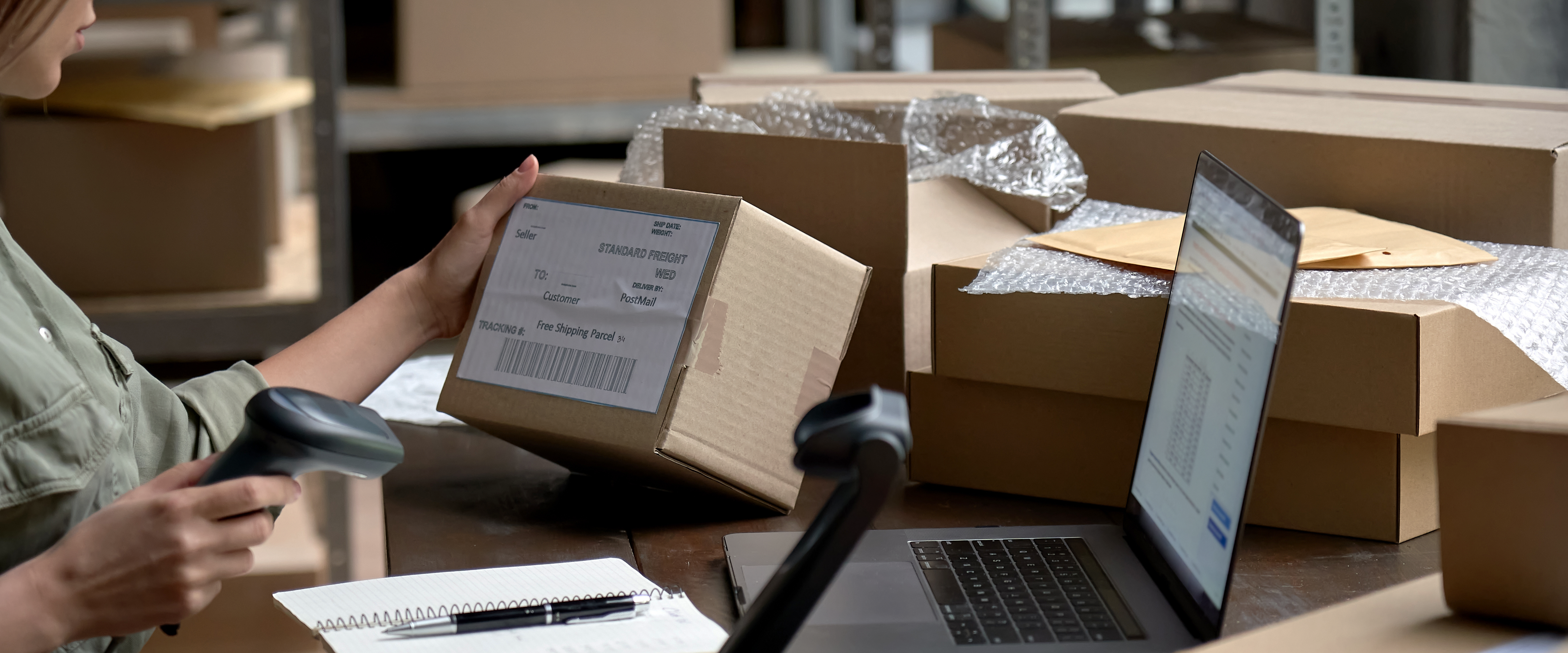
Inventory management can be a complex discipline where small inefficiencies quickly turn into major problems.
Many businesses struggle with slow and inefficient processes, where manual counting takes time, incorrect registrations lead to wrong deliveries, and employees waste valuable minutes searching for items on shelves.
Without a clear overview of inventory levels, businesses risk either overstocking – tying up unnecessary capital – or worse, running out of critical products, causing order delays and unhappy customers.
If you recognize some of these challenges, there is fortunately a solution – barcodes.
With a simple scan, you can significantly optimize your inventory management, minimize errors, and free up valuable time.
We have gathered 5 concrete ways barcodes can make a difference for your business. Read on to discover how you can take your inventory management to the next level.
1. Faster and More Accurate Registrations
Manual inventory management often comes with a high risk of errors. With barcodes, you can quickly and easily scan items upon receipt, movement, and dispatch. This reduces the risk of human error and ensures that your inventory data is always up-to-date. Additionally, it saves time for your employees, as they no longer need to manually enter information or double-check inventory lists.
2. Increased Efficiency in Picking and Packing
When your items are labeled with barcodes, your employees can quickly locate the right products and minimize errors in picking and packing. Using a handheld scanner or a mobile inventory management app, they can navigate the warehouse efficiently, ensuring a smoother workflow. This means fewer incorrect shipments, faster processing times, and an improved experience for both warehouse staff and customers.
3. Better Inventory Control and Less Shrinkage
Barcodes make it easy to track items in real-time, so you always know where your products are. This gives you better inventory control and helps reduce shrinkage and lost items. With precise data, you can quickly identify where problems occur and take proactive steps to minimize losses.
4. Simplified Reordering and Stock Replenishment
When items are scanned upon receipt and dispatch, your inventory management system (WMS) can automatically update stock levels and trigger reorder alerts when a product is running low. This ensures that you always have the right products in stock without tying up unnecessary capital in excess inventory. Automated reordering alerts also help you avoid delays that could affect deliveries and customer satisfaction.
5. Scalable Solution for Businesses of All Sizes
Whether you run a small webshop or a large wholesale business, barcodes can be integrated into your inventory management. They offer a flexible and scalable solution that can grow with your business. With a cloud-based inventory management system, you can customize features according to your needs, ensuring you only pay for what you use while still having the necessary tools as your business grows.
Easily Get Started with Barcodes in Your Inventory Management
Implementing barcodes does not have to be complicated. With an inventory management system like Rackbeat, you can quickly start scanning items via a mobile app or handheld scanner. This makes it easy to achieve a more efficient and error-free inventory management process.
Want to see how much time and hassle you can save? Try Rackbeat for free for 14 days and experience the benefits of digital inventory management with barcodes!