Lean Warehouse Optimization: How to Reduce Waste in Your Warehouse
By Rackbeat March 7, 2025
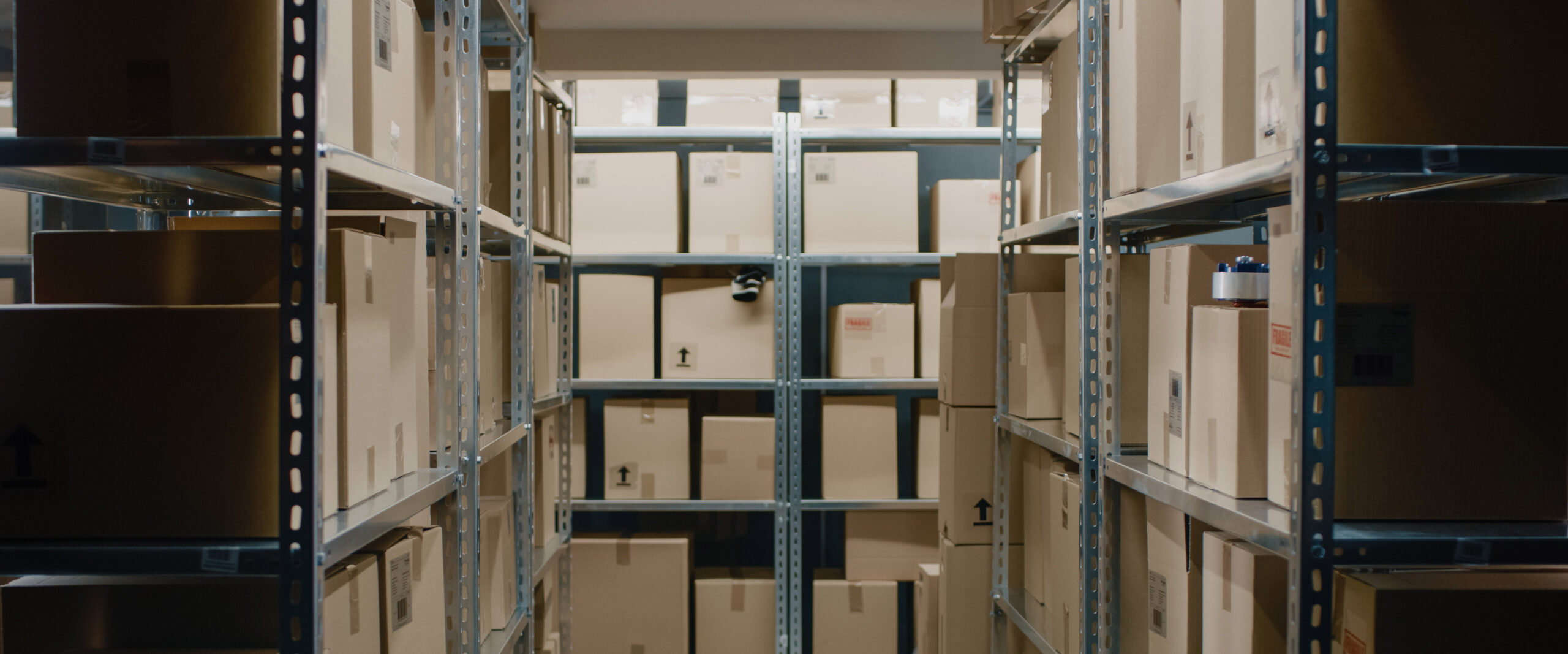
Are you struggling with unnecessary costs, space constraints, or slow work processes in your warehouse?
Whether you operate a wholesale business, an online store, a manufacturing company or a distribution center, waste in your inventory management can lead to unnecessary expenses and frustrated customers.
When employees waste time searching for products, and order errors result in returns, it directly affects your bottom line.
This is where lean warehouse optimization comes into play. The lean methodology helps you eliminate waste and ensures your warehouse operates like a well-oiled machine.
In this article, we dive into the most common types of waste in warehouses – and provide concrete methods to minimize them so you can save both time and money.
Read on – it’s not a waste of time.
The 7 Types of Waste in Warehouse Management
Within lean, seven types of waste are typically identified in warehouse management:
1. Overproduction – Producing or ordering more goods than necessary leads to unnecessary costs, a lot of tied up capital in the inventory, and the risk of product obsolescence. Producing based on demand helps avoid wasted resources on unsold goods.
2. Waiting Time – Employees or machines standing idle due to delays result in wasted time. This can be caused by delayed deliveries, slow systems, or inefficient workflows.
3. Unnecessary Transport – Moving goods too many times or over long distances increases time consumption and the risk of errors. If a product is moved around the warehouse unnecessarily, employees spend time on logistics instead of value-creating tasks.
4. Overprocessing – Performing unnecessary processes that add no value wastes time and resources. This includes manual data entry, duplicate order handling, or overly complex workflows.
5. Excess Inventory – Holding too much stock results in high storage costs and the risk of products becoming damaged or obsolete. A well-managed inventory ensures that only necessary stock levels are maintained.
6. Unnecessary Movements – Employees spending too much time retrieving or moving goods do not contribute to value creation. An optimal warehouse layout and efficient picking routes can reduce wasted time and improve the working environment.
7. Defective Products – Errors in products or orders requiring corrections or returns increase costs and delay deliveries. Quality control and precise processes can minimize errors and reduce return handling.
How to Reduce Waste in Your Warehouse
-
Implement a Warehouse Management System (WMS)
A digital warehouse management system (WMS) provides a clear inventory overview of your inventory, reduces human errors, and helps avoid overproduction. With real-time data, you can plan your warehouse operations more precisely and eliminate unnecessary waste.
-
Use the Just-in-Time (JIT) Principle
JIT ensures deliveries arrive exactly when needed, reducing inventory levels and waste. This method requires a well-coordinated supply chain but can result in significant cost savings.
-
Optimize Picking Routes and Warehouse Layout
Reduce unnecessary movements by placing the most in-demand items close to the picking area. Use zone picking and ABC analysis to identify the most efficient routes.
-
Automate Repetitive Tasks
Use handheld scanners for inventory management and conveyor belts or robots to minimize errors and reduce waiting time. Automation can increase speed and accuracy while allowing employees to focus on more value-creating tasks.
-
Standardize Work Processes
Establish fixed procedures for receiving, picking, and shipping goods to avoid slow and disorganized workflows. Standardization ensures consistency and higher operational quality.
-
Train Employees in Lean Principles
Engage your team in identifying and eliminating waste through continuous improvements. Involving employees in lean processes fosters a culture where optimization is a natural part of daily operations.
-
Analyze Data and Continuously Adjust
Use data from your warehouse management system to identify bottlenecks and inefficient processes. Ongoing analysis and optimization ensure that the lean approach remains central to warehouse management.
Become a Warehouse Expert with Our Newsletter
Want more practical tips and strategies for optimizing your warehouse? Sign up for our monthly newsletter, where we share the latest trends, tools, and best practices in warehouse management. Join hundreds of other warehouse managers and become an expert in lean warehouse optimization!