How to Optimize Your Manufacturing –
3 Tips to Avoid a Production Standstill
By Rackbeat December 13, 2023
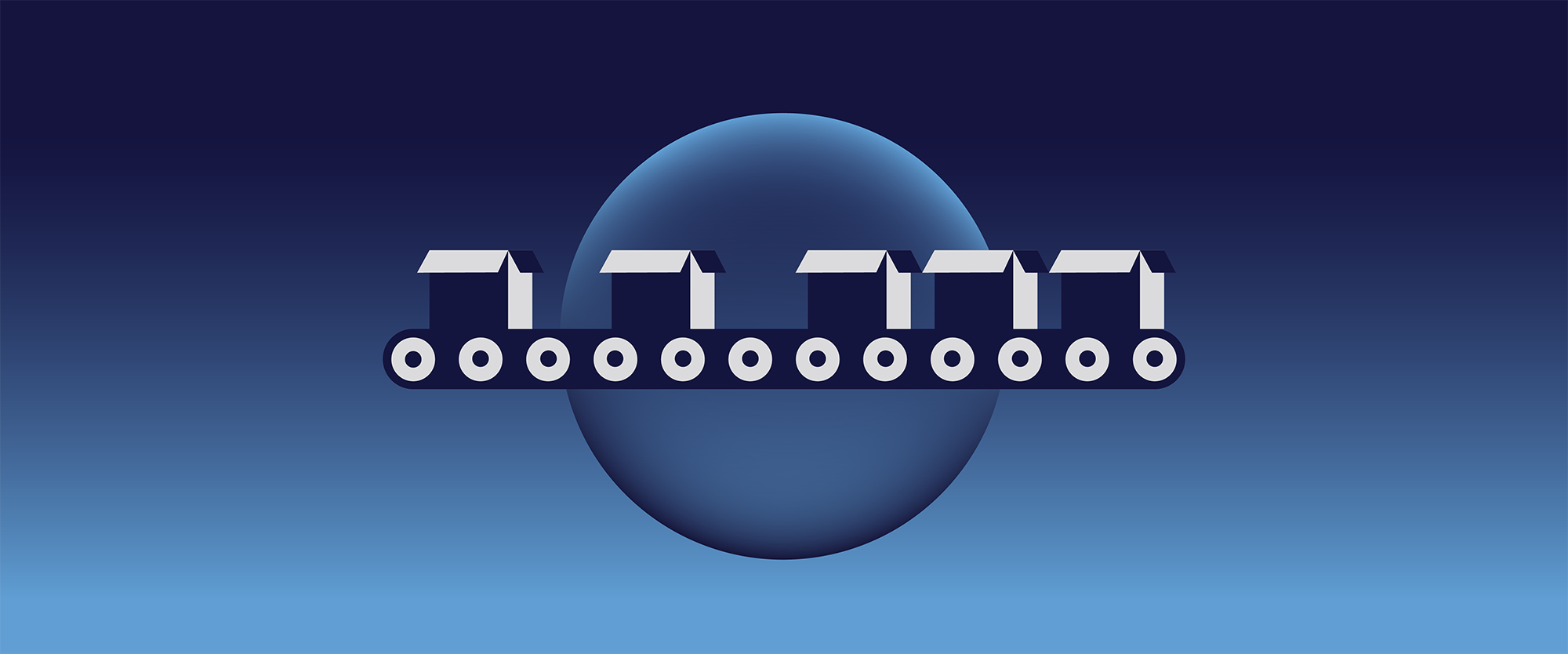
If there’s one thing that truly gives manufacturing managers gray hair during the day and nightmares at night, then it is production delays. After all, you largely depend on delivering the goods on time so that your customers are satisfied, spread the good word and return for more. That’s why it’s so important to minimize those painful periods when the wheels come to a halt.
Coincidences you can hardly guard yourself against can throw a wrench into the machinery – such as staff illness or a malfunctioning machine. But you do have areas where your direct involvement can determine whether the music stops on the production floor or if everything plays smoothly.
Therefore, we have gathered 3 topics that significantly impact whether your manufacturing is at risk of hitting a brick wall: Planning, flexibility and inventory management. By implementing the tips related to these topics, you will optimize your manufacturing processes and reduce periods of production halts.
1. Process Analysis and Planning: Streamline Your Manufacturing
The first thing you can do to optimize your manufacturing is to conduct a careful analysis and planning of all stages in the manufacturing process. By scrutinizing the different phases, you can rather easily optimize your manufacturing and identify possible causes of production halts.
When you lay out all the steps in the manufacturing process, you can, for example, look at systematizing the reception of raw materials, production line work, quality control, picking, packing and shipping. It would also be very conducive if you created a clear and updatable overview of things such as:
Who handles which production orders, when production starts and is expected to be delivered and where the different components are located in the warehouse.
Another thing that will streamline the planning of your manufacturing is to look at your resource allocation. That is – how resources such as labor, machinery and materials are used at each production stage. This allows you to assess whether you could, for example, redistribute some resources to achieve a better output.
The third, but perhaps most important, item on the agenda is identifying bottlenecks that can lead to a production standstill. And here, not having enough raw materials at your disposal is probably number 1 on the list of production obstacles. To overcome this challenge, ensure that you track the use of raw materials and set a minimum inventory quantity for each item. In doing so, you have a much better chance of ordering enough raw materials to assemble the finished product and delivering your production order on time.
Another thing needed to deliver the goods is flexibility.
2. Flexibility: Prepare for the Future
In a dynamic world with changing consumer habits, it’s a good idea to design your production processes with built-in flexibility. This allows you to quickly adapt to changes in demand or variations in the products your customers are seeking.
If, for example, you manufacture clothing, you know how quickly trends and consumer habits can change. Most companies in this sector have traditionally had a fixed production line that manufactures a specific range of clothing based on predictions about seasonal trends. However, as consumer preferences change very rapidly, traditional production methods are no longer sufficient in many cases.
One way a clothing manufacturer could implement a more flexible production structure is by investing in robot-based production cells that can be adapted to different sewing techniques and materials within minutes. This allows the company to switch production from one season trend to another without significant production stops.
You could also implement a digital monitoring system that analyzes data from social media and sales platforms to predict changes in consumer preferences.
Another area where flexibility is crucial is when it comes to price changes. It should be profitable for you to produce your finished goods, so you need to keep an eye on your suppliers’ prices and, if possible, diversify your supplier base. If you have multiple suppliers who can provide you with the same type of raw material, you reduce your vulnerability to supply chain and manufacturing bottlenecks.
Talking about bottles: You could call the last topic the ultimate bottle opener.
3. Solid Inventory Management: The Cornerstone of Successful Manufacturing
Effective and structured inventory management is crucial if you want to optimize your manufacturing and avoid production stops. No company can reach its full potential with inventory operations that rely on gut feelings or visual inspection. If you make purchases with your eyes closed, you risk either spending too much money on materials you can’t sell or you’ll have trouble keeping up with demand because you don’t make purchases in time.
Therefore, solid inventory management should be a top priority for you. There are two overarching tools you can use to implement effective inventory management.
The first can best be described as an inventory policy or a principle based on minimizing your inventory as much as possible. This principle is called “Just-in-Time” and involves acquiring the necessary materials right before you begin production. Yet, since it is mostly tied to manual inventory management via spreadsheets, which you have to update yourself constantly to get an accurate snapshot of the inventory, using Just-in-Time will inevitably result in you not always being able to purchase your raw materials in time.
Therefore, it is recommended that you use the second inventory tool if you want to obtain the most reliable inventory management that can feed your production in the right quantities. That tool is an automated inventory management software.
Inventory management software will tell you exactly what you have in stock in real time since it automatically updates your inventory when you receive new raw materials, use them in production and ship the finished product to a customer. It will even remind you to replenish with due diligence – that is before you run into a production standstill.
You can enter a minimum inventory quantity for each raw material involved in your manufacturing. The system will then notify you when the inventory limit for the product is reached, so you can order new raw materials immediately.
In summary, when you automate your inventory management, you will both reduce the risk of tying up too much money in materials you can’t sell again AND you will minimize costly production standstills.
But how do you get started with automating your inventory?
Avoid Production Halts with Rackbeat
Rackbeat’s cloud-based inventory system provides most of the functionality mentioned in this article. You can register raw material receipts, pick, pick & ship your production orders, diversify your supplier base with a supplier overview, get a detailed overview of all production orders and last but not least: Stay updated in real-time on your inventory and receive reorder reminders.
So, Rackbeat can help you avoid production halts and streamline your manufacturing processes. Read more about how Rackbeat’s inventory system can optimize your business here.