Lean inventory management: From theory to practice
By Rackbeat September 13, 2024
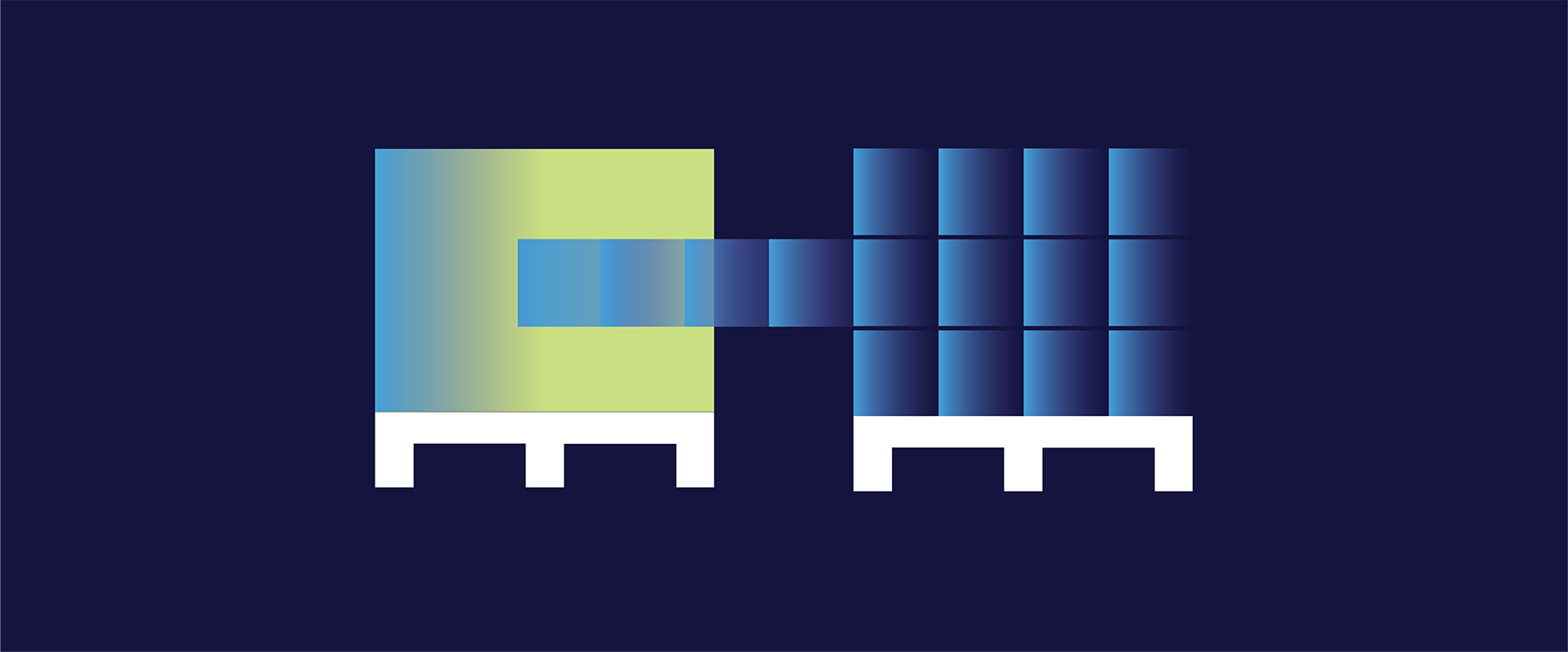
Lean inventory management is an approach to inventory management that aims to minimize waste and maximize efficiency. This method is based on Lean principles, originally developed in the automotive industry by Toyota, but now widely applied across various industries.
In this blog, we will dive into what Lean inventory management entails and how it can be implemented in practice.
What is lean inventory management?
Lean inventory management is about optimizing inventory processes to reduce waste and improve efficiency. Waste is a term within Lean that refers to all activities that do not create value for the customer. Waste can take many forms, including excessive stock, unnecessary workflows, and errors. By identifying and eliminating these forms of waste, companies can achieve significant improvements in productivity and customer satisfaction.
The five lean principles
Lean inventory management is built around five fundamental principles:
- Value: Identify what the customer demand is and what creates value for the customer, and focus on this.
- Value Stream: Map all the steps involved in delivering your product to the customer and identify activities that do not add value.
- Flow: Ensure that your products move smoothly toward the customer without interruptions or bottlenecks. JIT (Just-in-Time) can be considered the ultimate form of flow.
- Pull: Implement a pull system, where products are moving through the warehouse based on actual demand rather than forecasts, reducing stock levels and increasing turnover speed.
- Perfection: Make continuous improvements to ensure that inventory processes are optimized on an ongoing basis.
Implementing lean inventory management
Implementing Lean inventory management may seem straightforward, but it requires a systematic approach and a willingness to change both processes and culture to be successful. Here are some steps to get started:
-
Education and Training
The first step is to educate employees on Lean principles and their application in inventory management. This can include workshops, training programs, and hands-on exercises.
-
Value Stream Analysis
Conduct a value stream analysis to map out all processes in your inventory management. Identify where waste occurs and where there is potential for improvement.
-
Implement 5S
5S is a method for creating a more organized and efficient workplace. The five S’s stand for Sort, Set in order, Shine, Standardize, and Sustain. Implementing 5S helps establish order and reduce waste.
-
Use Kanban
Kanban is a tool that helps implement a pull system. It involves using visual signals, such as cards or boards, to manage production flow and inventory levels.
-
Continuous Improvement (Kaizen)
Kaizen is about continuous improvement through small, ongoing changes. Involve employees at all levels in identifying problems and developing solutions.
-
Technology and Automation
Modern technology can play a big role in Lean inventory management. Automating routine tasks and using data analytics can help optimize inventory management and reduce errors.
-
Measurement and Analysis
Set clear goals and KPIs (Key Performance Indicators) to measure the effectiveness of your Lean inventory management. Regularly analyze data to identify areas needing improvement.
Advantages of lean inventory management
- Reduced inventory costs by minimizing excessive stock.
- Increased efficiency and productivity through optimized processes.
- Improved customer satisfaction by delivering products faster and with fewer errors.
- Better working conditions for employees through more organized and safer work environments.
Disadvantages of lean inventory management
- Can lead to stock shortages if demand suddenly increases, as inventory levels are low.
- Depends on timely deliveries from suppliers, which can cause problems in case of delays.
- Without buffer stock, it can be hard to adapt to unforeseen changes in the market.
- Frequent small orders can increase shipping costs.
- External events, such as natural disasters, can have a significant impact on operations.
Lean inventory management and its associated principles can help to understand what is important and where your focus should be. At the same time, it requires a systematic approach during implementation, along with continuous focus, to ensure long-term success. However, Lean inventory management is not an “either-or” approach, but rather a set of principles that can each help you optimize your inventory processes.
Sign up and receive monthly tips and tricks for your inventory management directly in your email inbox!