Task management and inventory management: Discover how they complement each other
By Rackbeat October 18, 2024
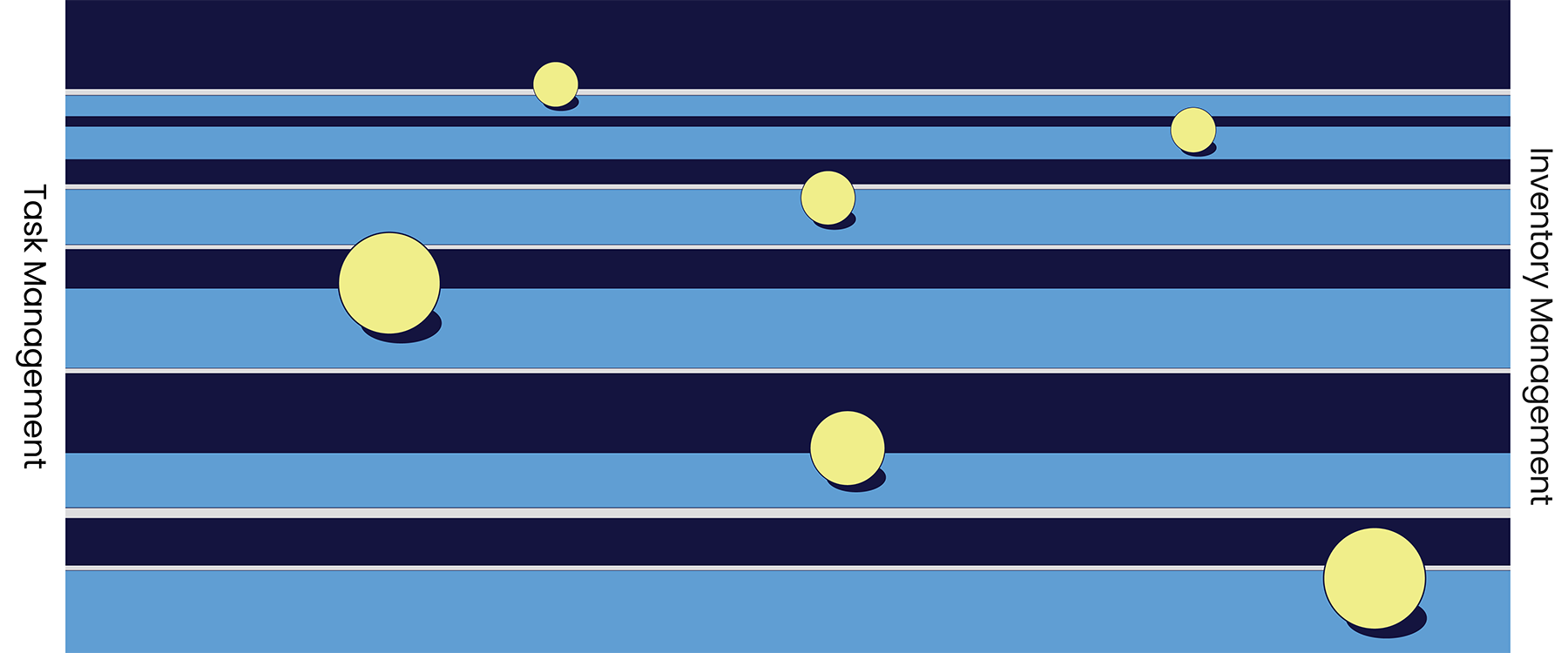
To run an efficient business, it’s crucial to have the right tools to manage every aspect of operations. Many companies focus on their top priority and implement a single key system. In doing so, they often overlook other tools that can complement the primary system and enhance efficiency even further. By using multiple systems in combination, businesses can gain a better overview, streamline workflows, and create even greater value for the business.
Two common systems in this context are task management and inventory management. While they are often seen as an either/or choice, there are significant benefits in connecting the two.
To understand how these systems can complement each other in practice, it’s important to first understand them individually and what sets them apart.
Task management
What is task management?
Task management involves organizing, tracking, and managing individual tasks or projects within a business. A task management system helps monitor each task from start to finish by ensuring that all necessary information is available and tasks are completed on time. With task management, businesses can effectively plan, prioritize, and allocate resources, ensuring that employees always have a clear overview of their tasks and deadlines.
Key features of task management:
• Task tracking: Track the status and progress of each task.
• Documentation and notes: Store relevant documents and notes related to tasks.
• Assignment and prioritization: Assign tasks to specific employees and prioritize based on importance.
• Reporting: Generate reports to gain insight into task status and resource usage.
Who benefits from task management?
Task management systems are ideal for businesses and organizations that handle many individual tasks or projects that require systematic follow-up and administration. This includes:
• Craftsmen: To manage tasks such as maintenance, repairs, and installation work, including planning, tracking, and documenting the work.
• Administration: To oversee resource use, registration, and quality assurance.
• Project managers: To keep track of project tasks and deadlines.
Inventory management
What is inventory management?
Inventory management focuses on monitoring, organizing, and optimizing a company’s stock operations. This includes tracking inventory levels, ordering new items, and ensuring that stock is neither overstocked nor understocked. An inventory management system ensures that products are available to meet customer demand without overloading stock with items that won’t sell.
Key features of inventory management:
• Inventory overview: Track the items in stock.
• Purchase management: Place orders when stock levels reach a certain threshold.
• Reporting: Gain insights into inventory status, sales data, and turnover rates.
• Integration: Integrate with sales and task management systems to optimize the entire supply chain.
Who benefits from inventory management?
Inventory management systems are crucial for businesses that handle physical products and need to keep their inventory updated. This includes:
• Craftsmen: To monitor materials and reduce waste.
• Retailers: To ensure popular items are always in stock and avoid ordering slow-moving products.
• Manufacturers: To track raw materials and finished goods during production.
• E-commerce businesses: To handle online orders and ensure fast, accurate delivery.
• Wholesalers: To manage purchasing and sales effectively.
While both task management and inventory management are essential for different types of businesses, their functions and applications are quite distinct. Task management is ideal for businesses handling many individual tasks and projects, while inventory management is indispensable for companies dealing with physical products and looking to optimize their stock operations.
For businesses that manage both individual tasks and physical products, combining task management and inventory management can be highly advantageous. Rather than choosing between systems, it’s beneficial to implement both, especially for craftsmen where tasks and materials are tightly interconnected.
Task and inventory management in a complementary solution
For a business to benefit from combining task and inventory management, there must be some interaction with physical products—otherwise, inventory management wouldn’t be relevant.
A good example of businesses that can benefit from this combination is craftsmen. These companies often use a task management system as their primary tool, providing an overview of tasks and allowing for time and material tracking.
By integrating inventory management with task management, craftsmen can have a complete overview of both stock levels and current tasks. This makes it easier to coordinate purchases with upcoming tasks, ensuring that necessary materials are available when employees need them and reducing the risk of delays.
Inventory management provides insight into which materials are available both in the main warehouse and in employees’ vehicles, detailing both quantity and type. This means that employees always know which materials are on hand and where they are located, allowing them to plan tasks more efficiently.
Additionally, materials can be transferred between vehicles, offering flexibility and control over material usage. The result is fewer delays, reduced waste, and an overall improved customer service experience.
For businesses managing individual tasks and handling physical products, combining task management with inventory management can be extremely beneficial. It ensures that operations run smoothly without unnecessary waste of resources.
Sign up and receive monthly tips and tricks for your inventory management directly in your email inbox!