Benefits of Automated Order Management for Your Warehouse Operations
By Rackbeat May 16, 2025
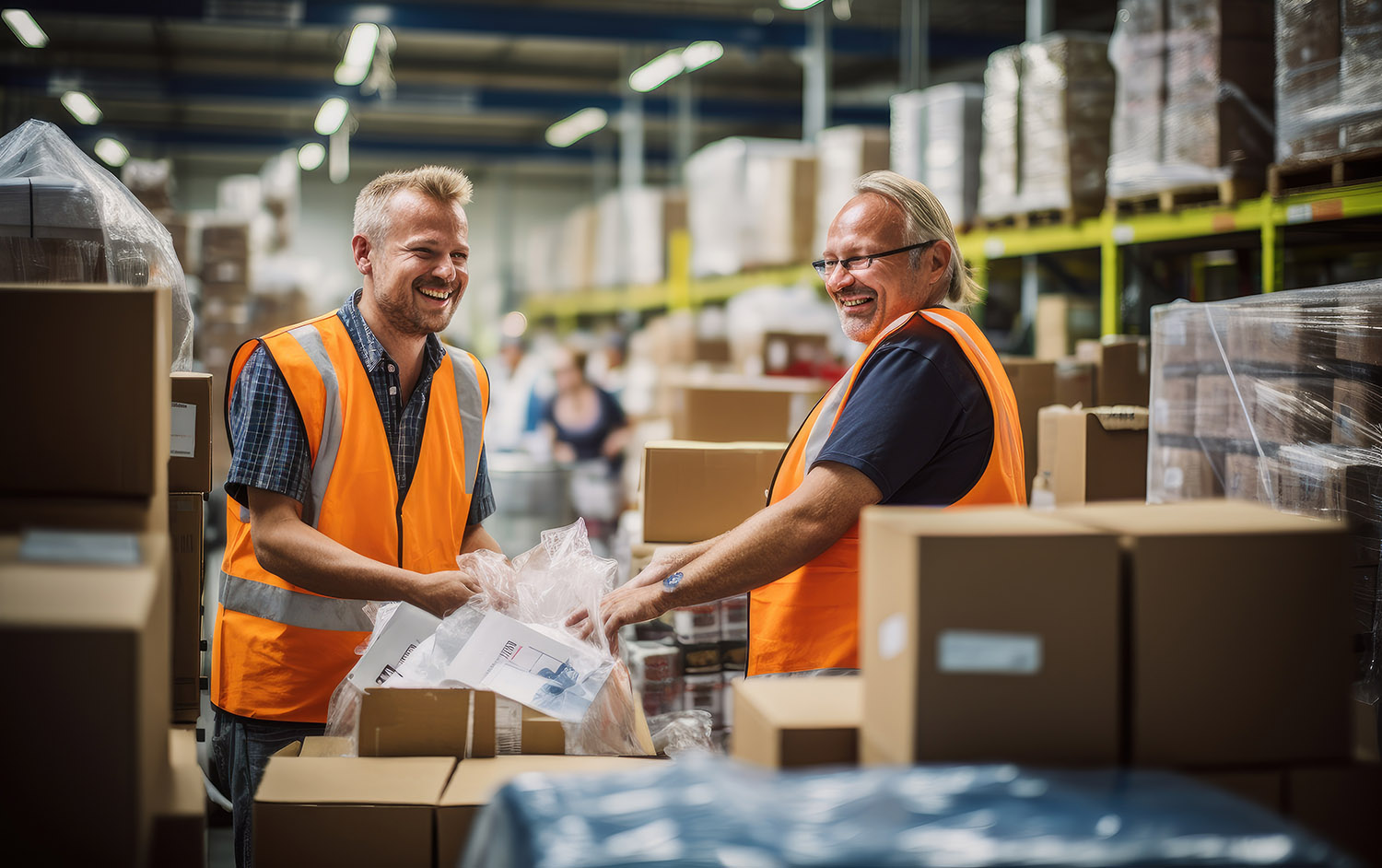
Does your order management feel like a game of Tetris, where everything crashes if one piece falls out of place?
Then maybe it’s time to give your workflows a technological boost.
By automating your order management – using, for example, a WMS, handheld scanners and connecting it to your existing systems – you can remove manual bottlenecks, minimize errors, and save valuable time.
That means fewer headaches. Faster order fulfillment. And more time for what actually grows your business.
But how do you get there?
In this article, you’ll get insights into:
-
What automated order management really means
-
Which specific benefits you can gain in your warehouse operations
-
How hardware like handheld scanners makes a real difference
-
And what it takes to implement the solution in practice
Whether you’re considering upgrading your current setup – or you’re simply curious about the possibilities – this article gives you a solid foundation to take the next step toward more efficient and future-proof inventory management.
What Does Automated Order Management Actually Mean?
When we talk about automation today, it’s easy to assume we mean advanced AI that predicts needs, moves goods, and runs the whole operation without human input.
But we’re not quite there yet.
Automated order management, as it looks today, doesn’t mean the system takes over every decision. It means you can eliminate manual, repetitive tasks and gain better control through technology that works with you – not instead of you.
It includes the following processes:
1. Automatic order processing:
Automated order management means orders can be received and processed without manual entry. This typically happens when a customer places an order in your webshop. At the same time, your stock levels are automatically synchronized with your warehouse management system – so you always have up-to-date inventory data.
2: Real-time inventory updates:
Inventory levels are updated instantly when goods are received or shipped, ensuring accurate warehouse control. This helps you avoid delays, double bookings, and delivery errors – because you always know what’s on the shelves and what’s not.
Real-time data also makes it easier to make fast decisions about purchasing, sales, and customer service, because you’re acting on current figures – not outdated estimates.
3. Purchasing management:
When your order flow is automated, purchasing becomes easier to manage – both in terms of timing and quantity. For instance, you can set up reorder alerts so the system notifies you (or automatically creates a purchase order) when stock drops below a set threshold.
That way, you avoid stockouts and last-minute orders – while also preventing overstocking that ties up working capital.
4. Integration with other systems:
Automated order management works best when it’s integrated with the rest of your business. By connecting it with your accounting software, webshop, or shipping platform, you ensure smooth data flow across systems and departments.
This means:
-
Orders can automatically generate invoices
-
Inventory movements are recorded in your accounting system
-
Shipping labels can be created directly from the order – with no extra clicks
5. Hardware: Handheld scanners and terminals as the key to efficient warehouse operations
To fully realize the benefits of automated order management, it’s crucial to invest in the right hardware to support and optimize warehouse processes. Handheld scanners, mobile terminals, and related equipment play a central role in ensuring accuracy and efficiency on the warehouse floor.
Examples of use:
-
Picking and packing: Handheld scanners guide employees through the picking process, ensuring the right items are picked and packed for the customer.
-
Goods receiving: When goods are received, scanners can quickly register and update inventory levels, speeding up the process and reducing errors.
-
Shipping: Before dispatch, scanners ensure that the correct goods are sent to the right destinations – improving customer satisfaction.
Implementing Automated Order Management
To successfully implement automated order management, companies should:
-
Choose the right WMS: A suitable Warehouse Management System (WMS) is crucial to support automation in the order process.
-
Integrate with existing systems: Ensure the selected solution integrates with your current ERP, accounting, and shipping systems.
-
Train your staff: Make sure your team is trained to use the new system effectively.
-
Monitor and evaluate: Ongoing monitoring and evaluation of the system’s performance is key to identifying areas for improvement and ensuring the automation delivers as expected.
Want to Learn More About Order Management? Get It Straight to Your Inbox
Automated order management isn’t just about efficiency – it’s a strategic investment in your company’s growth and resilience. By reducing errors, saving time, and connecting your systems, you free up resources to focus on what truly matters: delivering value to your customers and running a more profitable operation.
Implementation naturally requires some planning and a willingness to adapt – but the long-term benefits make it a worthwhile effort.
Want more actionable tips and inspiration on improving your warehouse, order handling, and overall business operations?
Then sign up for our monthly newsletter: